Glass-filled nylon, also known as PA GF, Nylon GF, or glass-reinforced nylon, is a versatile engineering thermoplastic. By incorporating glass fibers into nylon, this material achieves enhanced strength, rigidity, and thermal stability. It's also referred to as glass fiber-reinforced nylon, emphasizing the reinforcing element that transforms nylon's properties. These characteristics make it suitable for applications in industries like automotive, electronics, and consumer goods.
In this article, we'll explore glass-filled nylon in detail, covering its properties, manufacturing methods, advantages, and applications.
Material Properties of Glass-Filled Nylon
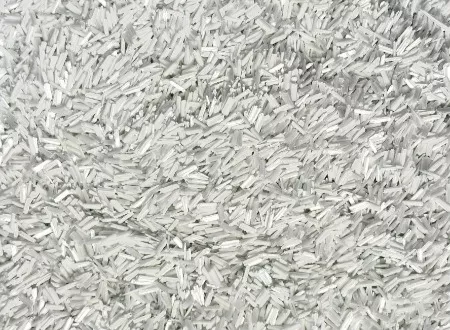
1. Increased Strength and Stiffness
The addition of glass fibers significantly boosts tensile and flexural strength, making glass-filled nylon suitable for load-bearing components.
2. Thermal and Dimensional Stability
Glass-filled nylon resists warping and deformation, even under fluctuating temperatures or high humidity. This makes it suitable for precision parts used in harsh environments, such as engine compartments.
3. Creep Resistance
Glass-filled nylon resists deformation under prolonged stress, ensuring long-term reliability in structural and mechanical applications.
Learn more: What is nylon?
What Is 30% Glass-Filled Nylon? And How Does the Percentage of Glass Filling Affect Nylon?
Glass-filled nylon is a composite material made by reinforcing nylon resin with a specific percentage of glass fibers to enhance its mechanical and thermal properties. The percentage—such as PA GF30, PA GF40, or PA GF50—represents the weight proportion of glass fibers in the material, with 30% glass-filled nylon (PA GF30) being one of the most popular grades due to its balanced strength, stiffness, and cost-effectiveness.
PA GF30 provides superior mechanical strength, resistance to creep and fatigue, and reduced warpage under normal conditions, making it ideal for a wide range of engineering applications. As the glass fiber content increases to 40%, 50%, or 60%, the material becomes stiffer and stronger but also more rigid and heavier, which may require specialized manufacturing techniques. Conversely, lower percentages like 15% or 20% glass-filled nylon offer basic reinforcement for applications prioritizing flexibility and lighter weight but may lack the rigidity needed for high-stress environments.
Understanding these percentage compositions is essential for selecting the right glass-filled nylon grade for your specific application. By carefully choosing the reinforcement level, you can achieve the perfect balance of performance and manufacturability for your project.
Read more about How To Replace Metal With Plastics.
Common Types of Glass-Filled Nylons
Glass-filled nylons are categorized based on the type of nylon resin used as the base and the percentage of glass fiber reinforcement. Below are the most common types:
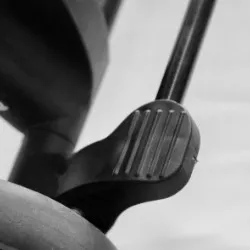
PA6 Reinforced with Glass Fiber (PA6 GF)
PA6 GF uses polyamide 6 (PA6) as its base resin. Also referred to as Nylon 6 or polycaprolactam, PA6 is known for its toughness and impact resistance, particularly at low temperatures. Glass fiber reinforcement enhances its mechanical strength and dimensional stability, making it suitable for a wide range of engineering applications. However, PA6-GF tends to absorb more moisture than other nylons, which can affect its dimensional accuracy in humid conditions.
10 Essential Insights on PA6 (Nylon 6) You Need to Know
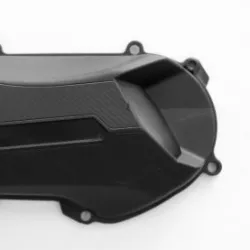
PA66 Reinforced with Glass Fiber (PA66-GF)
PA66 GF is based on polyamide 66 (PA66), also known as Nylon 66 or polyhexamethylene adipamide. Compared to PA6-GF, it provides greater stiffness, strength, and creep resistance, along with superior dimensional stability due to its lower moisture absorption. PA66-GF also exhibits excellent heat resistance, making it the preferred choice for high-temperature environments.
What is PA66 (Nylon66) - 8 Must-Know FAQs
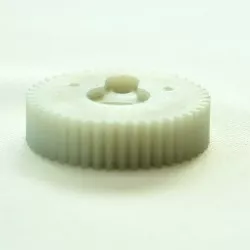
Low-Moisture Nylon Reinforced with Glass Fiber
For applications requiring extremely low moisture absorption, Low-Moisture Nylon is the material of choice. Its glass-reinforced structure enhances both dimensional stability and mechanical performance in humid environments. This makes it particularly suitable for industries demanding high precision, such as electronics, automotive, and metal replacement components. Low-moisture glass-filled nylon is frequently used for critical parts that require both thermal resistance and consistent dimensional accuracy, ensuring long-term reliability under challenging conditions.
Metal Replacement Nylon Polymers
Advantages and Disadvantages of Glass-Filled Nylon
Advantages
- Recyclability: Glass-filled nylon can often be recycled and reused in secondary applications, making it a more sustainable choice for industrial use.
- Enhanced Strength and Stiffness: Glass-filled nylon is significantly stronger than unfilled nylon, capable of withstanding high mechanical stress.
- Improved Dimensional Stability: Glass fibers reduce the coefficient of thermal expansion, minimizing warping and deformation under fluctuating temperatures.
- Creep Resistance: Glass-filled nylon resists deformation over time, even under prolonged stresses and elevated temperatures, making it ideal for structural and mechanical applications.
- Reduced Warping: Compared to unfilled nylon, glass-filled grades maintain their shape better in high-humidity or heat-exposed environments, improving precision and durability.
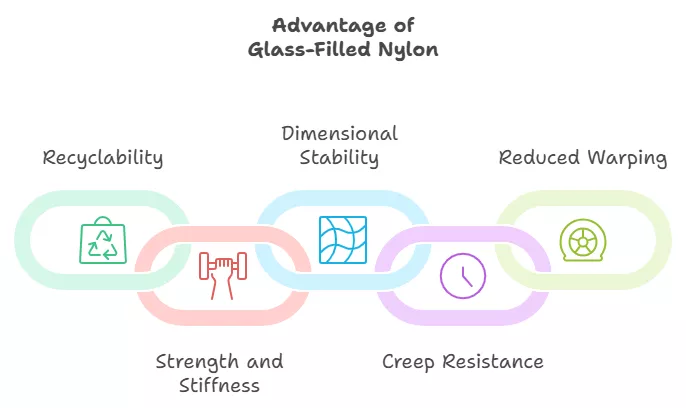
Potential Disadvantages
- Higher Brittleness: Purely glass-filled nylon can be less impact-resistant, making it susceptible to cracking under high strain.
- Processing Challenges: Without proper production conditions during injection molding, glass-filled nylon can exhibit surface fiber float, leading to a rough or uneven appearance that impacts the final product's aesthetic quality.
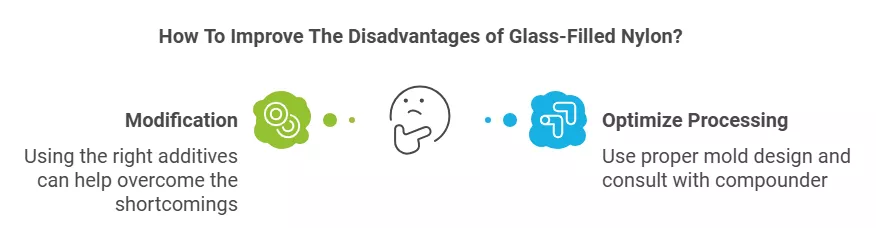
👉 Solution:
Nylon can be modified further with glass fiber + mineral fillers to reduce warpage or glass fiber + impact modifiers to improve brittleness. To address processing challenges, it's crucial to use a properly designed mold and consult with a compounder to determine the optimal processing procedures and temperature settings for glass-filled nylon. This ensures high-quality results both functionally and aesthetically.
Applications of Glass-Filled Nylon
Glass-filled nylon is widely used in various industries due to its exceptional properties:
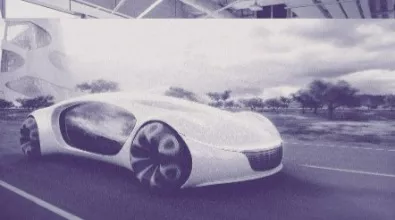
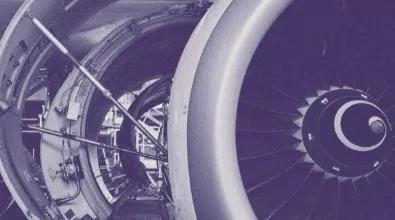
-
Industrial Equipment:
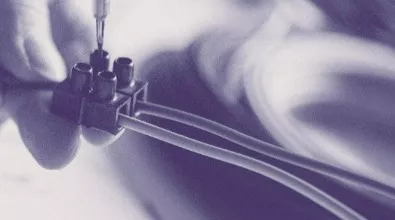
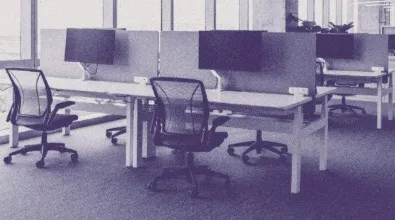
-
Consumer Goods:
Comparison of Glass Fiber Reinforced Nylon6 Products
PA6 GF30 |
PA6 GF40 |
PA6 GF50 |
PA6 GF60 |
|
Tensile Strength | 165Mpa | 185Mpa | 200Mpa | 220Mpa |
Elongation at Break | 3% | 2.8% | 2% | 2% |
Impact Strength (Notched) | 12 kJ/m² | 13 kJ/m² | 14 kJ/m² | 14 kJ/m² |
Density | 1.38 g/cm³ | 1.46 g/cm³ | 1.56 g/cm³ | 1.67 g/cm³ |
Comparison of Glass Fiber Reinforced Nylon66 Products
PA66 GF30 |
PA66 GF40 |
PA66 GF50 |
PA66 GF60 |
|
Tensile Strength | 180MPa | 200MPa | 215MPa | 235MPa |
Elongation at Break | 3% | 2.3% | 2% | 2% |
Notched Impact Strength | 13 kJ/m² | 14 kJ/m² | 14 kJ/m² | 15 kJ/m² |
Specific Gravity/Density | 1.38 g/cm³ | 1.46 g/cm³ | 1.56 g/cm³ | 1.67 g/cm³ |
Key Takeaways
Glass-filled nylon is widely used in various industries due to its exceptional properties:
-
Versatile Material: Glass-filled nylon, also known as PA GF or glass-reinforced nylon, offers enhanced strength, dimensional stability, and thermal resistance, making it ideal for demanding applications.
-
Customizable Formulations: Different grades and reinforcement levels, such as PA6 GF and PA66 GF, allow customization to address specific needs like warpage reduction (with mineral fillers) or improved flexibility (with impact modifiers).
-
Tailored Performance: The choice of reinforcement level, such as PA GF30, PA GF40, or PA GF50 glass-filled nylon, enables optimization of strength, stiffness, and processability for various applications.
-
Broad Industrial Applications: Widely used in automotive, industrial equipment, electronics, and consumer goods sectors, it meets diverse performance requirements from high heat resistance to lightweight durability.
-
Processing Considerations: Proper molding techniques and consultation with compounders are essential to ensure optimal production quality and avoid issues like surface fiber float.
Learn more about The Comparison of PA6 & PA66
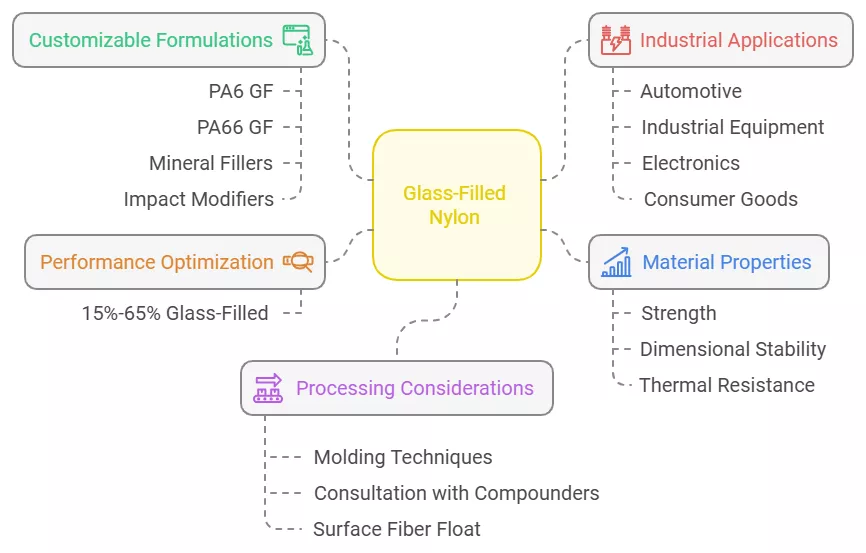
Case Studies: Scooter Manufacturer Speeds Ahead with Glass-Filled Nylon
A top scooter parts manufacturer was stuck with heavy, inefficient metal components:
The Starting Line:
- Engine Cover Rods:
- Rear Armrests:
These issues resulted in:
🚫 Increased production and maintenance costs
🚫 Reduced fuel efficiency.
🚫 Customer dissatisfaction due to durability concerns.
The Game-Changer:
- Solution: Switching to Glass-Filled Nylon.
- Material Innovation: Introduced a 30% glass-filled PA6.
- Customization: Tailored to meet strength and thermal requirements.
The Winning Results
🏎️ Performance Boost
- 40% Weight Reduction in engine cover rods and rear armrests.
- Improved acceleration and handling due to lighter components.
💪 Superior Durability
- Excellent resistance to heat and corrosion.
- Extended lifespan of parts, reducing the need for replacements.
💰 Cost Savings
- Lower production costs with easier manufacturing processes.
- Decreased maintenance expenses for end-users.
🌿 Eco-Friendly Impact
- Enhanced fuel efficiency leading to lower emissions.
- Contributed to sustainability goals.
Take Your Projects to the Next Level with Glass-Filled Nylon
Don't let outdated materials slow you down. Embrace innovation with glass-filled nylon and experience:
- Customized Solutions: Materials tailored to your exact needs.
- Expert Support: Guidance from concept to production.
- Competitive Edge: Stand out with superior products.
Looking for reliable glass-filled nylon materials for your application? At All Around Compounding (All Around Polymer Co., Ltd.), we specialize in customized formulations of PA GF to meet specific requirements. Contact us to learn more about our products or to request a sample for your next project!