Did you know that over 90% of modern headlight housings rely on engineered thermoplastics for optimal performance? As vehicles evolve with advanced lighting systems like LEDs and laser lights, the choice of materials for headlight housings has become more critical than ever. Selecting the right material not only enhances structural integrity but also ensures thermal resistance, chemical stability, and an aesthetic finish.
In this article, we will guide you through the key considerations for selecting headlight housing materials and explore the top-performing options, including Nylon with Mineral Filler, Polybutylene Terephthalate (PBT), and Nylon-6 Nanocomposites.
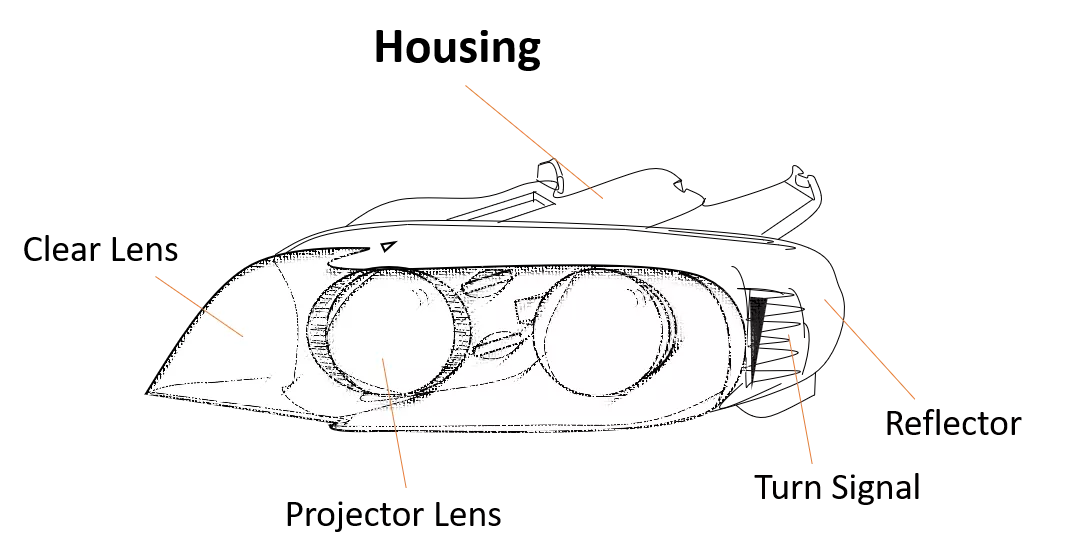
Automotive Headlight Housings
Choosing the right materials is vital for reducing manufacturing defects, optimizing injection molding cycles, enhancing moldability, extending tool life, and reducing weight for better fuel efficiency. These factors collectively influence both the quality and economics of production.
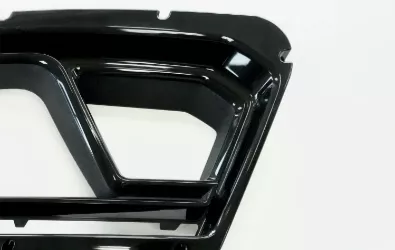
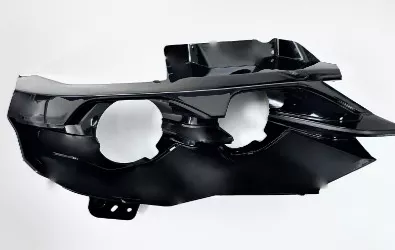
Key Considerations for Headlight Housing Materials
When selecting materials for headlight housings, understanding the application demands is crucial. Here are the most important factors to consider:
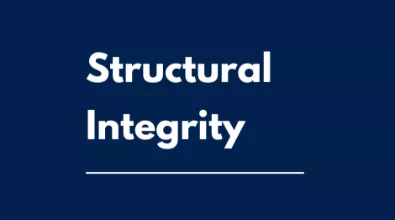
-
Structural Integrity
The car headlights must endure road vibrations and potential impacts without cracking or warping. For example, mineral-filled nylon provides enhanced rigidity, making it ideal for heavy-duty applications in rugged terrains.
-
Thermal and Electrical Properties
Modern headlights, especially those with LEDs and laser systems, can reach temperatures exceeding 100°C. Materials like Nylon-6 Nanocomposites, with their exceptional heat deflection temperatures, maintain shape and performance under these extreme conditions.
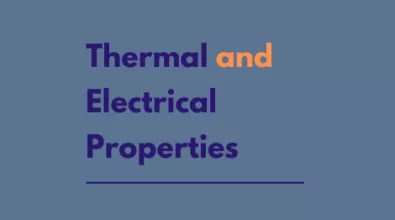
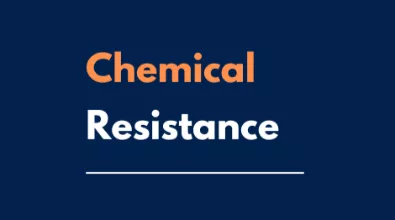
-
Chemical Resistance
Headlight housings often come into contact with automotive fluids, such as engine oils and cleaning agents. PBT offers superior chemical resistance, preventing discoloration and degradation over time.
-
Injection Molding Dynamics
Complex shapes demand materials with high fluidity for seamless mold filling. For instance, Nylon with Mineral Filler improves moldability and reduces defects, making it ideal for intricate designs.
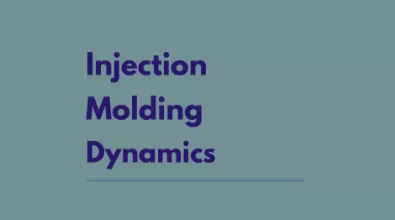
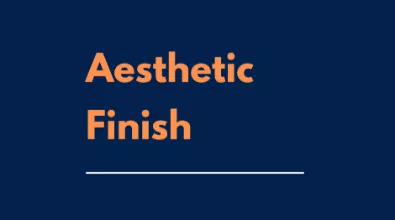
-
Aesthetic Finish
Electroplating compatibility is essential for achieving the polished, metallic look preferred in luxury vehicles. Nylon-6 Nanocomposites allow direct electroplating, eliminating additional coating steps and ensuring a sleek finish.
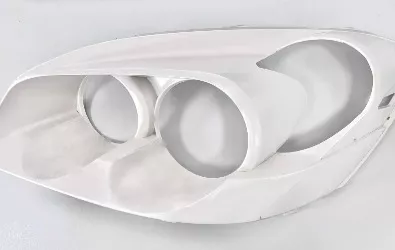
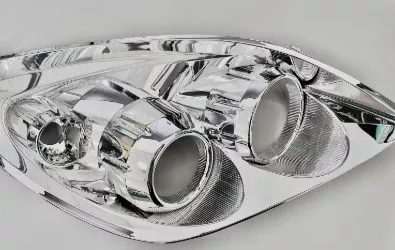
Headlight housing BEFORE and AFTER electroplating
Best Material Choices for Car Headlight Housing
1. Mineral Filled Nylon
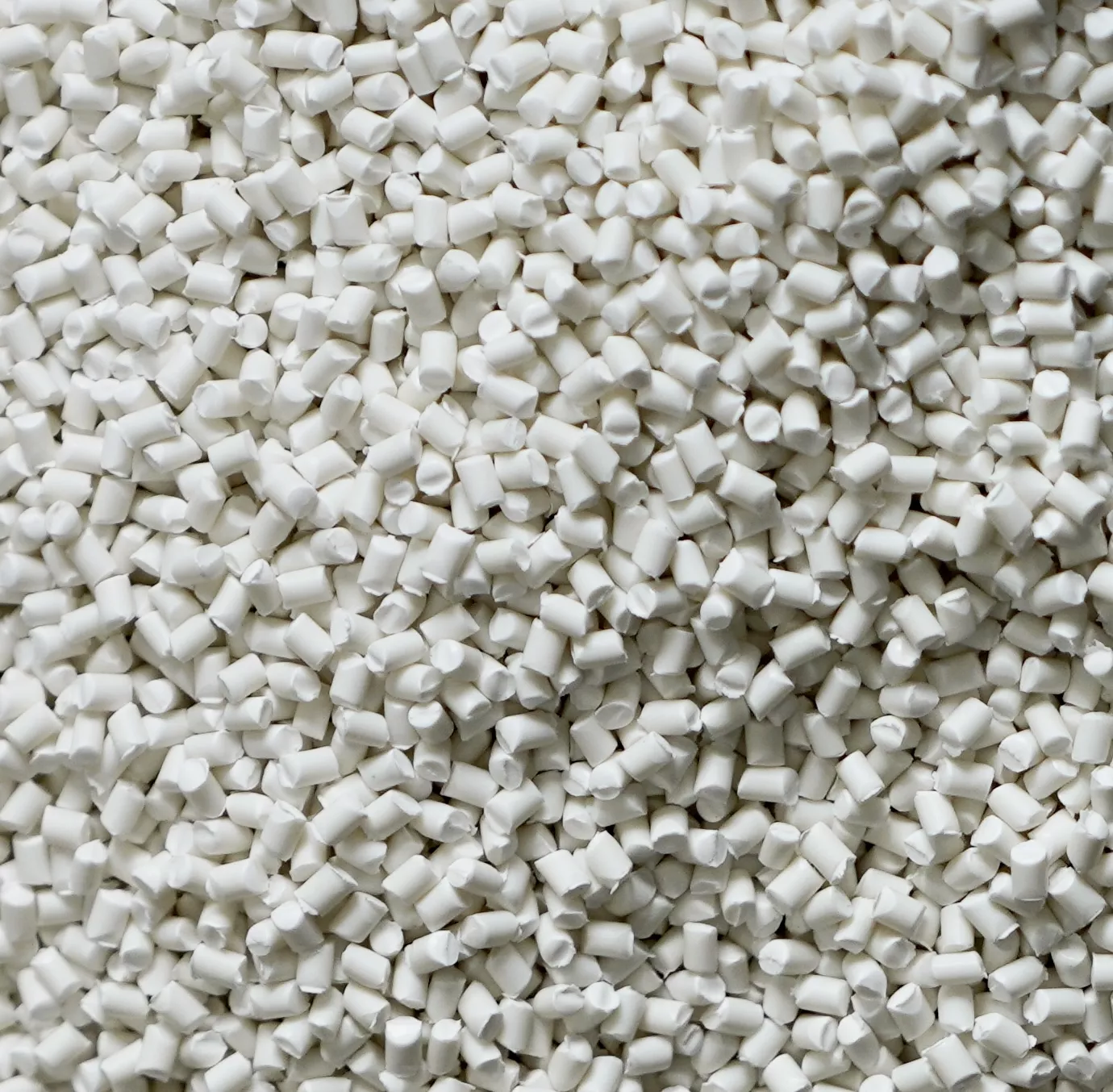
Advantage
Superior dimensional stability, reduced warpage, and excellent thermal resistance. The addition of mineral fillers enhances the fluidity of nylon, making it an excellent choice for intricate injection molding processes.
Ideal For
Applications requiring high rigidity and resistance to deformation under heat.
Comparison
Compared to other options, mineral-filled nylon provides the best balance of cost and performance for general use.
2. Polybutylene terephthalate (PBT)
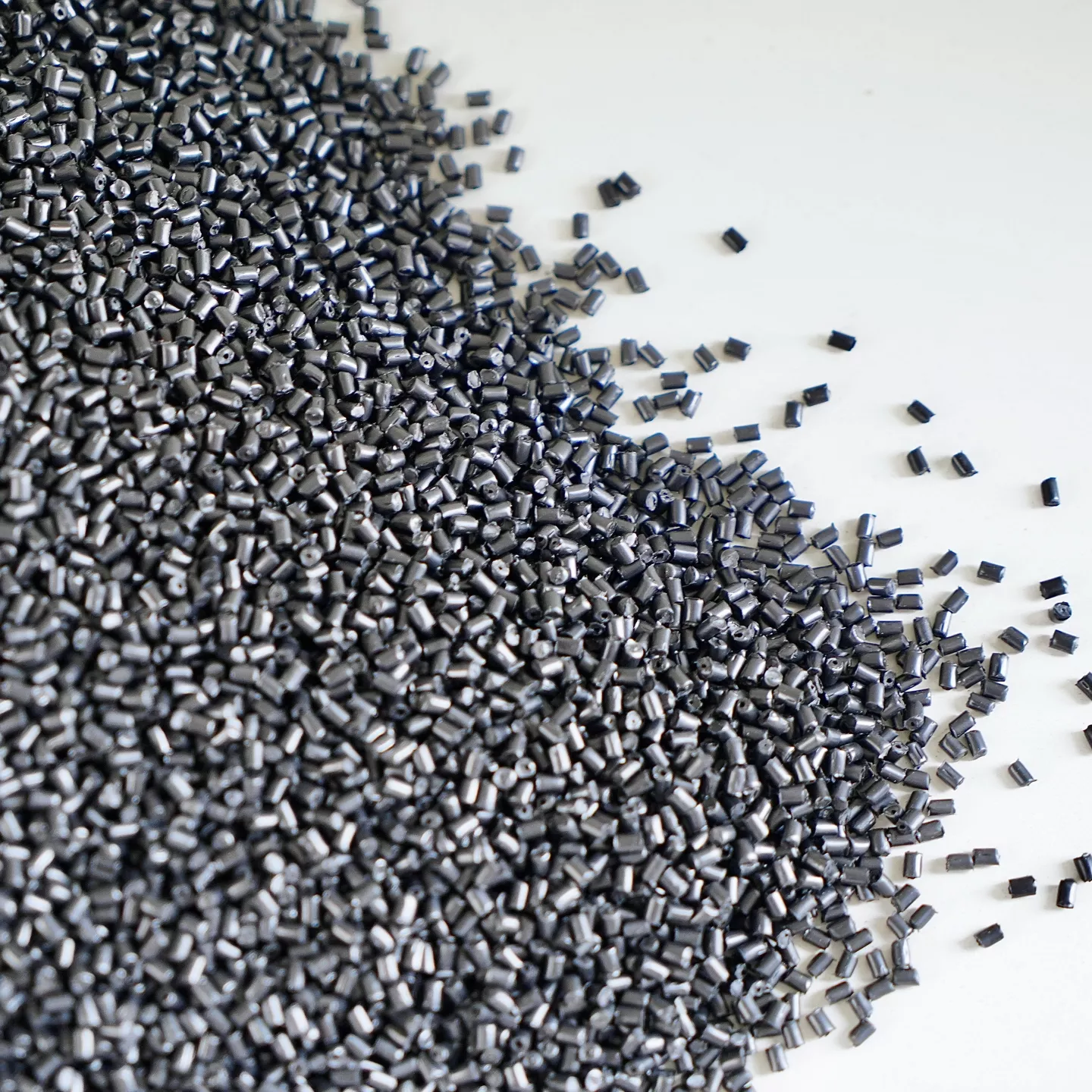
Advantage
Outstanding chemical resistance and superior surface finish. PBT efficiently fills mold cavities, creating precise and well-defined headlight base components. It also offers excellent dimensional stability.
Ideal For
Components requiring a high degree of aesthetic appeal, such as visible headlight parts. PBT is inherently compatible with electroplating processes, allowing for polished, metallic finishes that enhance the headlight base's visual appeal.
Comparison
While PBT offers better chemical resistance, it may be more brittle than mineral-filled nylons in high-impact areas.
3. Nylon-6 Nanocomposite
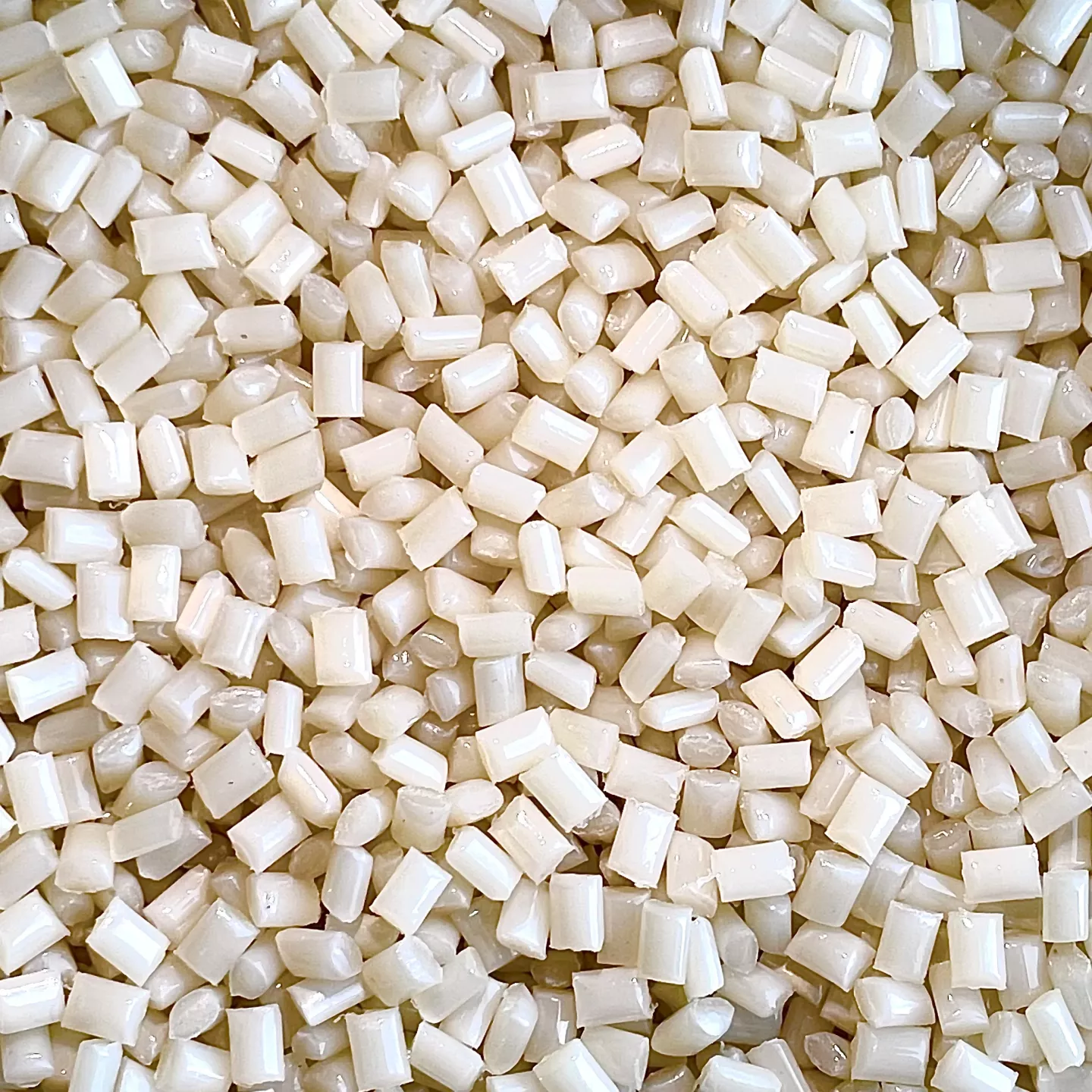
Advantage
Exceptional heat deflection and tensile strength, making it ideal for heavy-duty use. Nylon6 Nanocomposite materials can be directly electroplated without the need for coating, due to its unique properties.
Ideal For
High-performance headlights with extreme thermal requirements. Nylon6 nanocomposite materials help save multiple post-manufacturing processes represents a forward-thinking solution for manufacturers aiming to streamline operations, maintain quality standards, and minimize environmental impact.
Comparison
This Nylon6 nanocomposite material outperforms standard mineral-filled nylon in extreme environments but comes at a higher cost.
Headlight Housing Material Comparisons
Material |
Strength |
Heat Resistance |
Chemical Resistance |
Surface Finish |
Cost |
Mineral-Filled Nylon |
High | High | High | Good | Moderate |
Polybutylene Terephthalate (PBT) |
Moderate | Moderate | High | Excellent | Affordable |
Nylon-6 Nanocomposites |
Very High | Very High | High | Excellent | Higher |
Innovating Headlight Housing: A Story of Transformation
The Challenge
In the highly competitive automotive market, a leading headlight manufacturer faced a pressing challenge: delivering high-performance headlight housings for premium vehicles while streamlining their production process. Traditional materials such as mineral-filled nylon could no longer keep up with the growing demands for:
- Extreme thermal resistance to accommodate high-powered LED and laser light systems.
- A sleek, electroplated surface without adding costly coating steps.
- A production process that minimized waste and supported sustainability goals.
Their engineers needed a solution that was not just effective but transformative.
The Breakthrough
We suggest to do trial with our supportive product—Nylon-6 Nanocomposites—a cutting-edge material known for its exceptional heat resistance and tensile strength. But what truly set it apart was its direct electroplating capability. Unlike traditional materials, this headlight material eliminated the need for additional coating processes, offering a perfect synergy between performance and efficiency.
Working closely with the client's R&D team, we reimagined their manufacturing workflow:
- Thermal testing: Proven performance in extreme conditions with 20% higher than standard requirements.
- Injection molding adjustments: Fine-tuning to achieve consistent dimensional stability.
- Electroplating trials: A seamless transition from molding to electroplating without intermediate steps.
The Result
The adoption of Nylon-6 Nanocomposites was a game-changer:
- Performance Leap: The housings effortlessly handled temperatures generated by advanced LED systems, withstanding prolonged use without deformation.
- Manufacturing Redefined: By eliminating the coating step, production times were reduced by 20%, significantly increasing throughput.
- Aesthetic Excellence: Electroplated housings showcased a flawless finish, elevating the design appeal for luxury vehicles.
- Environmental Impact: Fewer production steps translated to lower energy consumption and material waste, aligning with the client’s sustainability commitments.
Looking Ahead
“By adopting Nylon-6 Nanocomposites, we didn’t just improve our product—we transformed our process”
Said by The Client's Lead Engineer.
This collaboration not only solved the immediate challenges but also paved the way for future innovations in headlight manufacturing. With a forward-thinking approach, Nylon-6 Nanocomposites empowered the client to achieve their goals while setting a new benchmark in the industry of headlight materials.
Why Choose All Around Compounding for Your Material Needs?
At All Around Compounding, we understand that every application has unique demands. With decades of expertise and data-driven solutions, we offer customized materials designed to optimize performance and aesthetics for car headlight housing.
Conclusion
Selecting the right material for car headlight housings involves balancing performance, cost, and manufacturing efficiency. Whether you need the rigidity and thermal resistance of Mineral-Filled Nylon, the chemical stability and surface quality of PBT, or the cutting-edge performance of Nylon-6 Nanocomposites, each option offers unique advantages.
Take the Next Step: Explore Our Material Solutions
At All Around Compounding Co., Ltd. (All Around Polymer Co., Ltd.), we specialize in providing advanced materials tailored to your specific needs. From improving production efficiency to meeting stringent performance requirements, our solutions empower manufacturers to innovate with confidence. Contact us today to explore how our materials can transform your next project.
Partner with us to unlock the full potential of advanced materials and elevate your automotive components to new heights of performance and durability. Contact us at info@aaccl.com or download our catalog for comprehensive information.