When it comes to high-performance engineering plastics, nylon composite materials are an excellent choice. Nylon (Polyamide, PA) boasts remarkable mechanical strength, wear resistance, and chemical resistance, making it popular across industries such as automotive, scooters/motorcycle, electronics, and industrial equipment. By incorporating reinforcing materials like glass fiber, carbon fiber, mineral powder, or elastomers, nylon composites can enhance strength and rigidity while also adjusting other properties like heat resistance, moisture absorption, and impact resistance.
What makes nylon even more versatile is that it can be reinforced with multiple additives simultaneously, such as glass fiber plus impact modifiers or glass fiber plus mineral fillers, allowing you to achieve highly tailored results. Whether you're looking to boost impact resistance, improve surface finish, or reduce warpage, we have the expertise to combine the right additives and develop materials that meet your exact requirements.
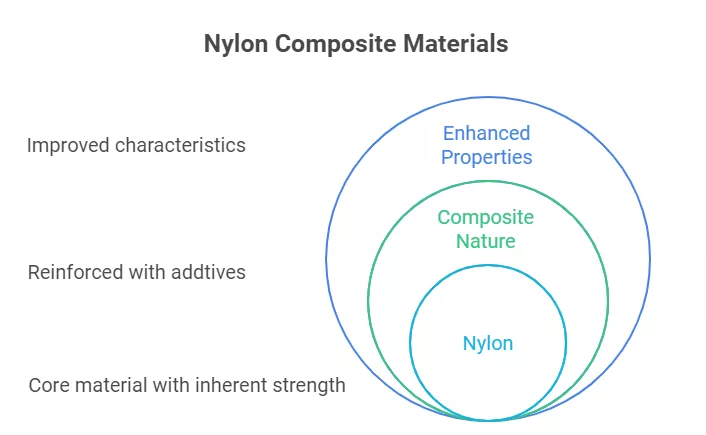
6 Main Types of Nylon Composite Materials
1. Glass-Fiber Reinforced Nylon
Glass fibers dramatically improve the rigidity and dimensional stability of nylon, making it suitable for high-strength applications such as automotive components, power tools, and industrial machinery parts. This enhanced strength and stability also make glass-fiber reinforced nylon an ideal solution for metal replacement, offering a lightweight yet durable alternative that maintains the performance required in demanding environments.
2. Carbon-Fiber Reinforced Nylon
Carbon fibers enhance both strength and rigidity while reducing material weight, making this composite ideal for industries that demand lightweight solutions, including aerospace, high-performance automotive components, scooter and bicycle components, metal replacement components and sports equipment.
3. Mineral-Reinforced Nylon
Adding mineral powder boosts rigidity and fluidity while maintaining cost-efficiency. This type is commonly used in electronic devices, automotive headlight components, and consumer product enclosures.
Discover the best material for automotive headlight housing: How to Select Automotive Headlight Housing Materials.
4. Impact Resistant Nylon
Enhanced with elastomers or rubber, impact-modified nylon offers superior impact resistance, making it well-suited for applications like automotive bumpers, industrial machinery, sports gear, and electronic enclosures.
Find out how the right impact modifiers can boost nylon's durability and flexibility by clicking here.
5. Heat-Resistant Nylon
Specially treated to withstand higher temperatures, heat-resistant nylon is ideal for parts operating in demanding, high-temperature environments, such as engine components, home appliances and industrial machinery.
Read more features about our heat-resistant nylon product
6. Low-Moisture-Absorption Nylon
Low-moisture-absorption nylon is designed to mitigate the issue of water absorption, making it perfect for humid environments, including electronic products, automotive parts, outdoor equipment, and any components where high dimensional stability is critical.
Explore the key features of our Low-Moisture-Absorption Nylon, designed for optimal performance in humid environments.
Advantages of Nylon Composite Materials
Nylon composites offer exceptional versatility and can be precisely customized to meet the specific demands of various applications. Whether your project requires high strength, lightweight performance, chemical resistance, or impact resistance, nylon composites deliver flexible and cost-effective solutions.
With their multifunctional properties and enhanced dimensional stability, these materials are suitable for a wide range of industries, ensuring reliable performance in even the most demanding environments.
So, Why Choose Nylon Composite Materials?
- Versatility: Suitable for various industrial applications.
- Cost-Effectiveness: Customizable to boost economic benefits.
- Stability: Enhanced processing ensures excellent dimensional stability and impact resistance.
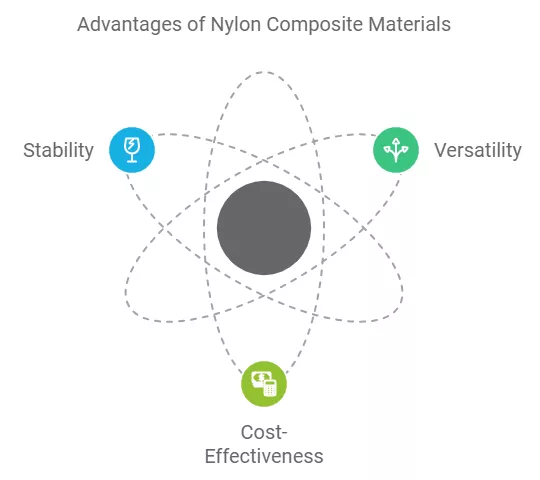
However, What Makes Nylon More Than Just Nylon?
While nylon composites are known for their versatility, it's the ability to tailor them to specific needs—through the addition of glass fibers, impact modifiers, and mineral fillers—that truly sets them apart. Nylon becomes more than just a material; it transforms into a solution engineered for the most complex challenges. Let's look at some real-world examples of how we've customized nylon to meet our clients' unique requirements.
Case Studies: Demonstrating Our Expertise in Tailored Nylon Solutions
-
Case Study 1: Multi-Additive Reinforced Nylon for Metal Replacement in Automotive Components
A leading automotive manufacturer approached us with a challenge: replacing heavy metal parts with a material that could offer similar strength, better fuel efficiency, and corrosion resistance. After analyzing their needs, we recommended a glass-fiber reinforced PA66 nylon composite combined with an impact modifier for added toughness.
Solution: We worked closely with their engineering team to customize the nylon material, ensuring it met their performance specifications, including withstanding high temperatures under the hood and absorbing impacts without cracking.
Outcome: The solution led to a 30% reduction in weight, improving fuel efficiency by 15% and reducing production costs. Our multi-additive approach allowed the client to achieve their performance goals, and they are now exploring additional metal-replacement opportunities with us.
-
Case Study 2: Low-Moisture-Absorption and Mineral-Filled Nylon for Electronics Housings
An electronics manufacturer faced challenges with their previous material due to warpage from moisture absorption, which caused frequent product returns in high-humidity environments.
Solution: We proposed a low-moisture-absorption nylon composite, reinforced with mineral fillers and glass fiber to improve rigidity and surface finish. This combination helped maintain product dimensions and ensured long-term durability even in humid conditions.
Outcome: The client saw a 40% reduction in product returns and an extended product lifecycle by 20%. Our ability to combine multiple additives into one material provided the perfect solution, cementing the client's confidence in our expertise.
Discover How We Can Customize Nylon Solutions for Your Unique Challenges
At All Around Compounding, we understand that nylon is far from simple. With our expertise, we can combine glass fiber, impact modifiers, mineral fillers, and more to create the perfect material blend for your application. Whether you need enhanced strength, reduced warpage, or improved impact resistance, our knowledge of multi-additive formulations allows us to develop nylon solutions tailored to your exact specifications.
Contact us now for engineered solutions that are as complex or straightforward as your project requires. Our team is ready to customize nylon composite materials that meet your performance needs across industries.